Strength Behind Titanium Forging: What Makes It So Powerful?
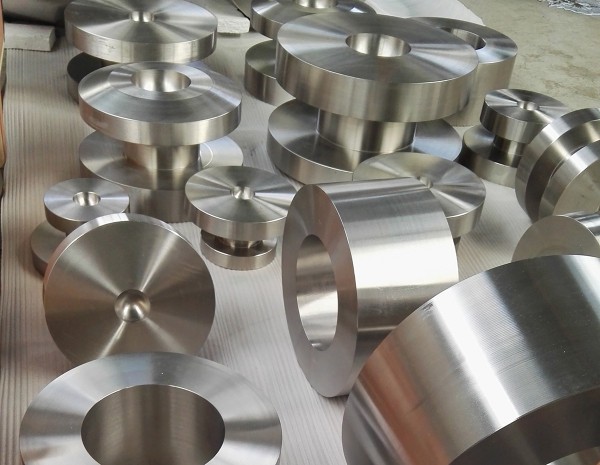
Titanium forging is a critical process in manufacturing components for industries where strength, durability, and precision are non-negotiable. From aerospace and medical applications to automotive and marine engineering, forged titanium parts offer unmatched performance in extreme conditions. But what exactly makes titanium forging so valuable, and why is it preferred over other metals or manufacturing methods?
What Is Titanium Forging?
Titanium forging involves shaping titanium metal using compressive forces at high temperatures. This process refines the metal’s grain structure and aligns it in the direction of the part’s stress points, significantly enhancing its mechanical properties. Unlike casting, where molten metal is poured into a mold, forging produces parts that are denser, stronger, and more resistant to fatigue and corrosion.
Benefits of Titanium Forging
1.Superior Strength-to-Weight RatioTitanium is renowned for its exceptional strength-to-weight ratio. Forging further enhances this characteristic, making titanium components ideal for high-performance environments like aircraft engines or high-speed automotive parts where every gram matters.
2.Corrosion Resistance
One of titanium's standout properties is its resistance to corrosion, particularly from salt water and bodily fluids. This makes forged titanium the material of choice for medical implants, marine parts, and chemical processing equipment.
3.Enhanced Structural Integrity
The forging process compresses the metal’s internal structure, eliminating voids and reducing porosity. This leads to greater structural integrity and longer service life, especially in applications that experience repetitive stress or harsh operating conditions.
4.Heat Resistance
Titanium retains its strength at elevated temperatures, making forged titanium parts suitable for applications such as jet engine components, where performance and safety are paramount.
Titanium Forging of Common Applications
●Aerospace: Forged titanium parts are used in landing gear, turbine components, and structural airframe elements.●Medical: From hip and knee implants to surgical instruments, titanium forging ensures strength, precision, and biocompatibility.
●Automotive: Performance vehicles often incorporate titanium forgings in suspension systems, engine valves, and exhaust components.
●Industrial & Marine: Pumps, valves, and propeller shafts benefit from titanium’s corrosion resistance and mechanical strength.
Titanium Forging Processes
Several forging techniques are used depending on the complexity and specification of the component:●Open Die Forging: Ideal for large, simple shapes. The metal is compressed between flat dies, allowing flexibility in dimensions.
●Closed Die Forging (Impression Die): Used for more complex shapes with tight tolerances. The metal is placed in a die shaped like the final product and hammered into form.
●Isothermal Forging: The die and metal are maintained at the same temperature, reducing stress and improving metal flow, ideal for aerospace-grade components.
Conclusion
Titanium forging is more than just a manufacturing method—it’s a gateway to high-performance, long-lasting parts in some of the world’s most demanding environments. Its blend of lightness, strength, and resilience makes it indispensable for advanced engineering challenges. Whether it's a life-saving implant or a critical aircraft component, titanium forging ensures safety, reliability, and performance where it matters most.